So...I cut around the tube carefully just at the line that ran around the strut (seemed as good a place as any)
Then the insert simply pulls out
Looking inside the JA strut, it's machined and the machining finishes about 8mm down inside the tube. So I figured that when it gets welded I'll use the thicker part to weld to for that extra bit of security.
I chopped the JA strut down to this line.
Before I started chopping up the VN strut, I put the insert in and measured the distance from the top of the insert to the top of the sleeve, it measured 1.8mm (I'll use 2mm)
Then I put the nut on, tightened it up to see how close the nut is to the thread...measured about 3mm. But the only number I need is 2mm for this exercise.
I then put the insert into the JA sleeve and measure the amount of insert sticking out.
It measured 31mm. So....31mm (to the top of the insert) + 2mm (cos the sleeve sits 2mm higher than the insert top) = 33mm, this becomes the length of my new sleeve. I've rough cut them, next job is to cut them down to the right height. You'll also notice the machined step inside the VN sleeve, the cut will be below the sleeve in the thicker part.
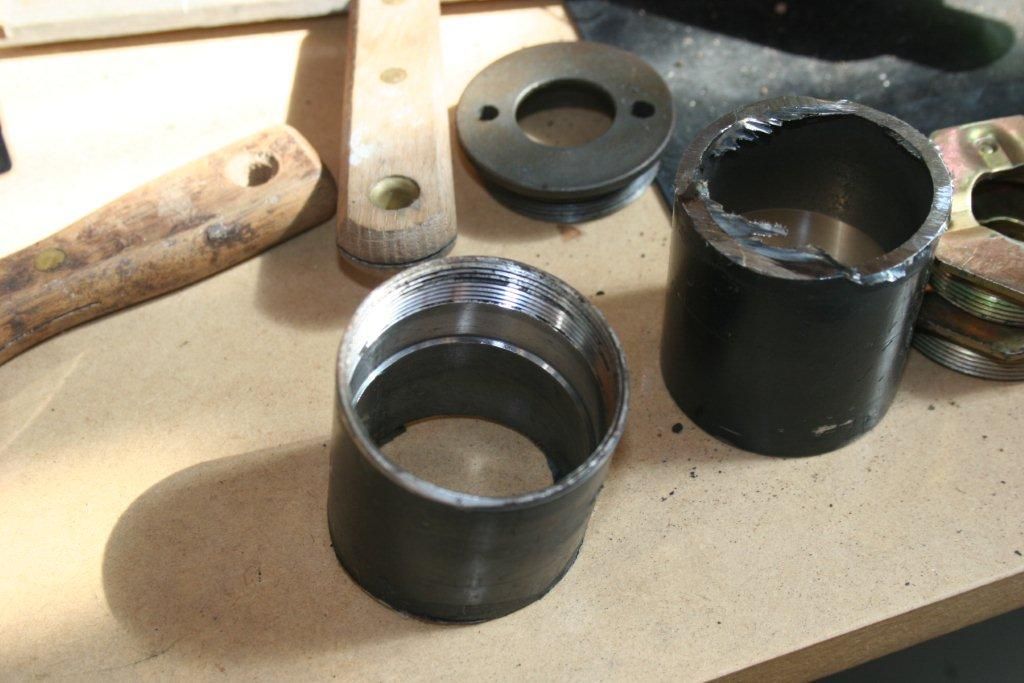